Root cause analysis (RCA) involves searching backwards from an undesirable effect (or problem) to its cause(s) and addressing those causes. While the term “Root Cause” implies that there is a single cause for a problem, more often multiple causes interact and work together to trigger the problem. The RCA task is to identify potential causes, determine which cause or causes are root causes and address those root causes to ensure the effect (the problem) does not recur. RCA is important because if a problem has occurred once, it most likely will occur again.
However, if the root cause is found and addressed, future occurrences of the same problem CAN BE PREVENTED! RCA and corrective action is the key to preventing future problems.
Root cause analysis tools will be shared during this session, Evaluating corrective or preventive action and process will also be discussed.
Areas Covered in the Session :
- Establishing an effective team environment
- Clarifying what the problem is and what the problem is not
- Searching for the root cause by investigating the problem’s symptom(s)
- Using data and investigative tools to identify the root cause(s)
- Employing decision making to select the most appropriate solution
- Initiating measurements to ensure the problem does not reoccur
- Recognizing common barriers to RCA and how to overcome them
Who Should Attend:
- QA Managers and Engineers
- Manufacturing Managers and Engineers
- Consultants
- Quality System Auditors
- Safety and Quality Auditors
- Project and Program Management Teams
- Operations Management Teams
- Executives and Managers responsible for investigating and solving problems
Course Director: LANCE B. COLEMAN
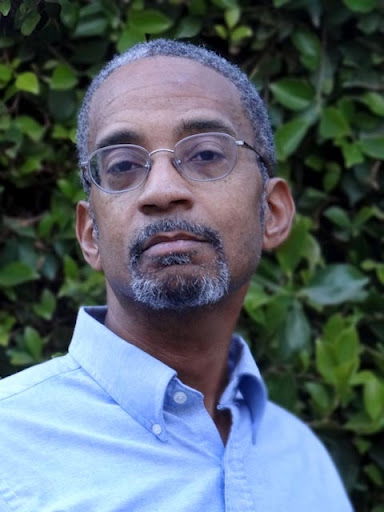 | Lance B. Coleman has over 20 years of leadership experience in the areas of quality engineering, Lean implementation, quality and risk management in the Medical Device, Aerospace and other regulated industries. He has a degree in Electrical Engineering Technology from the Southern Polytechnical University in Marietta, GA and is an American Society for Quality Senior Member as well as, Certified Quality Engineer, Six Sigma Green Belt, Quality Auditor and Biomedical Auditor. He is also an Exemplar Global Principal QMS Auditor.
Lance is Chair of US TAG 302 – guidelines for auditing management systems as well as a voting member of US TAG 176- quality management and quality assurance. He is the author of “Advanced Quality Auditing: An Auditor’s Review of Risk Management, Lean Improvement and Data Analysis (Quality Press 2015)” and “The Customer Driven Organization: Employing the Kano Model (Productivity Press 2014)”, as well as many articles on quality, risk management and Lean implementation.
Additionally, Lance is an instructor for the ASQ Certified Quality Auditor Exam Preparatory and FMEA courses. As Principal Consultant of Full Moon Consulting, he has presented, trained and consulted throughout the United States and abroad.
|
|
|
|